原油开采过程中,不可避免地会伴随一定量的水分。原油含水对炼油反应的影响不容忽视。将深入探讨原油含水 4% 时对反应的影响,帮助炼油企业优化工艺,提高生产效率。
原油含水对反应的影响
原油含水对炼油反应的影响主要体现在以下几个方面:
- 催化剂失活:水与催化剂接触后会发生吸附,阻碍催化剂活性位点,降低催化剂活性,影响反应速率和转化率。
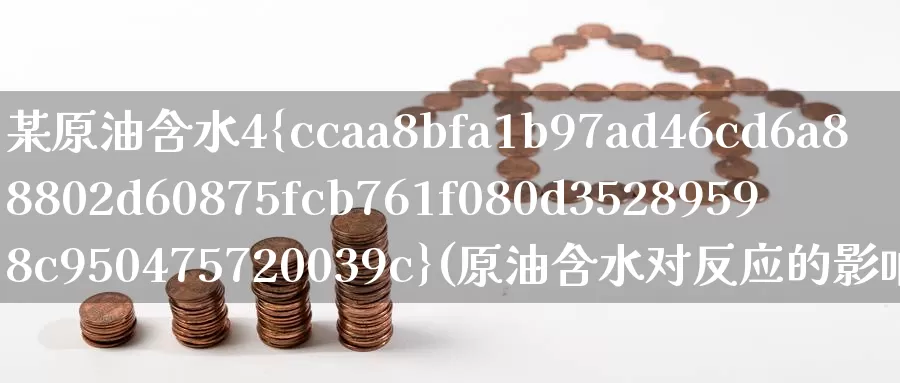
- 反应产物质量下降:水的存在会改变反应环境,导致反应产物质量下降,如汽油辛烷值降低、柴油十六烷值降低等。
- 设备腐蚀:水与原油中酸性物质反应,产生腐蚀性物质,对炼油设备造成腐蚀,缩短设备使用寿命。
- 能耗增加:水的存在会增加反应体系的热容量,导致反应所需的能量增加,从而提高能耗。
原油含水 4% 的影响
当原油含水量达到 4% 时,其对反应的影响尤为明显:
- 催化剂失活加剧:4% 的含水量会显著增加催化剂失活的程度,导致反应速率大幅下降,影响生产效率。
- 反应产物质量严重下降:高含水量会严重影响反应产物质量,导致汽油辛烷值下降至不可用水平,柴油十六烷值降低,影响发动机性能。
- 设备腐蚀加剧:4% 的含水量会加速设备腐蚀,缩短设备使用寿命,增加维护成本。
- 能耗大幅增加:高含水量会增加反应体系的热容量,导致反应所需的能量大幅增加,加重企业能耗负担。
应对措施
为了减轻原油含水 4% 对反应的影响,炼油企业可以采取以下应对措施:
- 原油脱水:在炼油前对原油进行脱水处理,去除水分,降低含水量至可控范围。
- 使用抗水催化剂:采用抗水催化剂,减缓催化剂失活,提高反应效率。
- 优化反应条件:调整反应温度、压力等条件,减轻水分对反应的影响。
- 加强设备维护:定期对设备进行维护,清除腐蚀物,延长设备使用寿命。
原油含水 4% 对炼油反应的影响不容忽视。它会导致催化剂失活、反应产物质量下降、设备腐蚀和能耗增加。炼油企业应采取有效的应对措施,如原油脱水、使用抗水催化剂、优化反应条件和加强设备维护,以减轻水分对反应的影响,提高生产效率和产品质量。